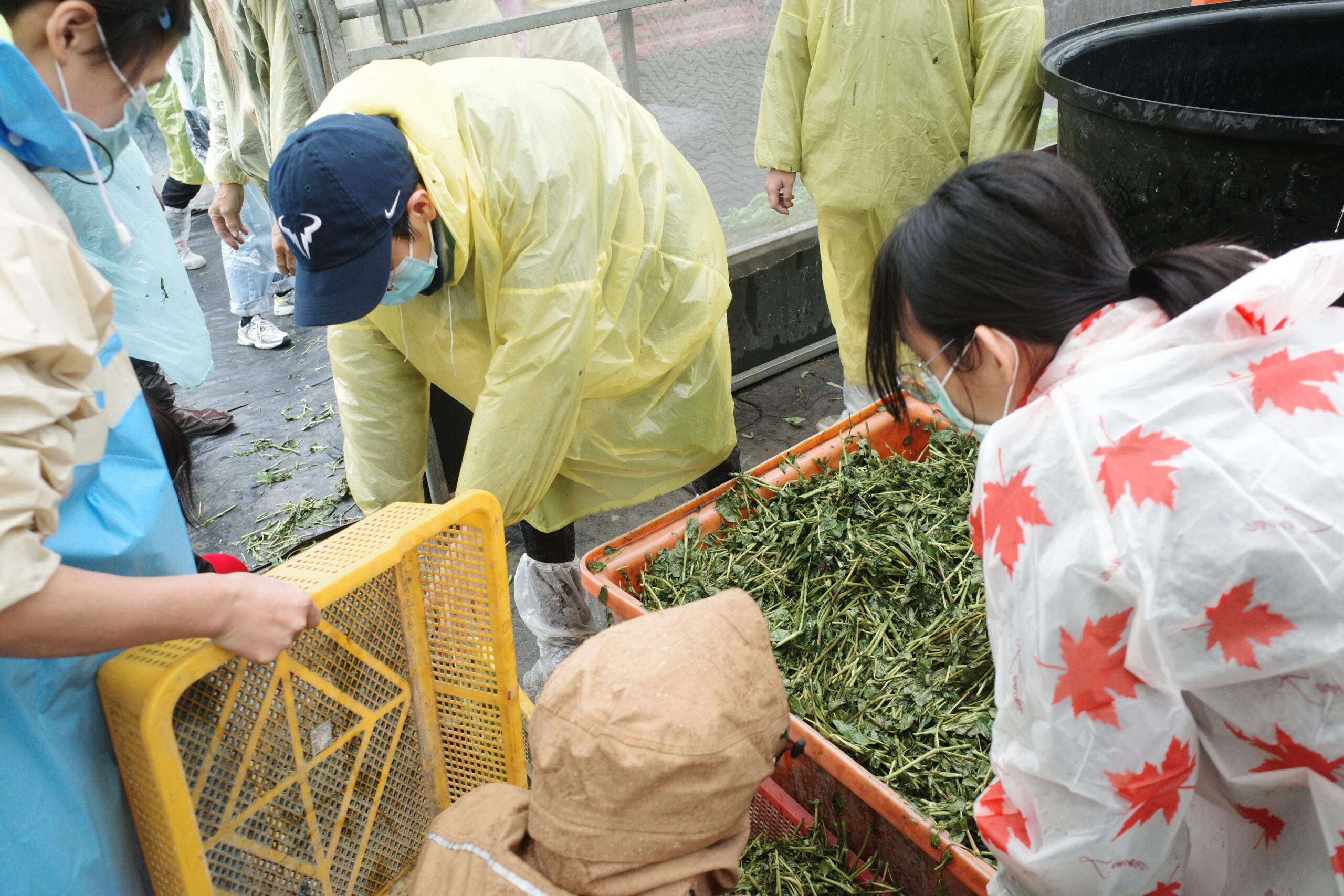
南投田野調查-學生田調心得
活動名稱:南投田野調查
課程教師:江明親、張懿文
課程講師:湯文君、鄭司政
課程助教:林安琪
活動地點:南投自然色農場及工坊
活動時間:111年04月02日(六)- 04月03日(日)
【IMCCI學生田調心得】
We really didn’t know what to expect from this trip, other than a rainy weekend, lots of blue and the amazing opportunity of participating in a workshop led by the Taiwanese indigo artist, Wen-Jun Tang. It took us almost five hours to get to Nantou, where the National Taiwan Craft Research and Development Institute is located, the place where we would spend the following four hours learning about the art of Indigo dyeing. Hanging on the room’s ceiling were dyed fabrics, towels and different kinds of clothes with astonishing designs; this was the room where the magic happened. At the back corner were two big plastic orange boxes filled with Indigo vat.
Wen-Jun Tang, with the assistance of the English translator Regina Yu-ching Lin, explained the process of Indigo dyeing. First comes the harvest of Indigo plants. Then, the leaves are soaked in water in a tank for one week; this step is called “precipitation”. After this, they make the Indigo vat. This is the hardest step because it depends on the experience and the skill of the artist to create a good quality vat. Many ingredients can be used to produce it, such as wood ash, sea shells and lime. The vat is fed with honey, sugar or other nutrition sources depending on the country, tradition, etc.
The dyeing process employs many different techniques; this workshop focuses on stencil technique, originated from Japan. We created patterns over silk fabric using stencil boards or by hand, with pasting powder, which can be made from rice or soy beans. We used rice pasting powder in this workshop. This material is created by mixing water, plain rice and sticky rice powder and boiling it for 30 to 40 minutes. After this, lime or seashell are added and stirred in a pot, until it becomes pasty.
After the pattern was created, we added wood dust over the paste to prevent it from sticking to other materials and hung it. Before soaking it into the vat, we sprayed water on the fabric. The artist mentioned that we should soak the fabric for 3 minutes and later take it out and wait for it to turn from green to blue, before soaking it again. However, the soaking time varies depending on the color the participants want to accomplish. When you are content with the color, you wash the paste out and dry the fabric with a towel.
【建文所學生田調心得】
這天我們來到南投草屯的國立臺灣工藝研究發展中心,很榮幸的可以聽到湯文君老師分享藍草的種類、介紹型糊染技法,並引導我們親手製作或使用型板上糊和染色,是特別且深刻的體驗。
| 藍草種類 |
在臺灣最常聽到藍染使用的藍草是木藍和山藍,但其實還有更多的藍草種類,如蓼藍、菘藍和芙蓉藍。單是屬蓼科的蓼藍,在中國、韓國和日本就擁有二十種。
常以為藍草只能用於染色,但其實還有藥用的功能。相信不少人聽過的中藥材「板藍根」,其實就是長得像「油菜花」的菘藍之俗稱。因屬性寒,能清熱解毒,治風熱感冒,常用來當作中藥材。尤其在換季的天氣,更是容易患感冒之人的良藥。
至於芙蓉藍,是臺灣較少見的藍草。因屬熱帶的爬藤類,常見於馬來西亞,特色在於其色素含量最高。聽湯老師說,芙蓉藍的葉子能長到像臉一樣大,和其他藍草相比更是與眾不同。
| 型糊染 |
介紹完藍草後,湯老師和鄭大哥為我們說明型糊染的材料與技法。型糊染是藍染的防染技法之一,利用膏狀的糊料作圖或刻版複印,讓膏體停留的部分不會染上染料,在織品上呈現圖案。型糊染的糊料,依不同地區的做法分為兩類:中式的黃豆糊與日式的糯米糊。本次文君老師採用能立即染色的糯米糊讓我們進行嘗試。除了工坊內已刻印好的型版,老師還貼心的準備了包裝成錐狀的糊料,像是做蛋糕時的擠花,讓我們能自由創作、大展身手!
畫糯米糊時要特別注意糊在布面的沾附,糊料一定要滲入布裡,不能浮在布上。畫完圖案之後,趁糊料還未全乾,將布的背面噴濕以固著糊料,接著在正面的糊料上灑上木屑,固定圖案,即可將作品放入染缸中進行染色。
雖然本次只操作型糊染的塗糊、染色,文君老師為我們介紹糊料製作與建藍製靛。糊料製作需秤量材料比例調製麵糊,待蒸熟後添加石灰、海鹽,打製到油亮才能開始使用;染缸則是需經過靜置、打藍、建藍等步驟。有了自然色農場繁複的前置作業,才能讓我們可以順利的體驗,讓大家都收穫美麗的成品,也讓我們更期待明天的行程!